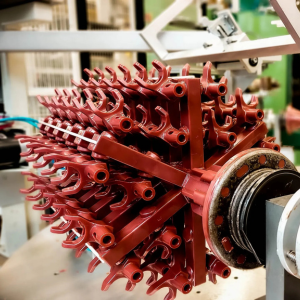
Wax Injection Process
There are many ways for starting of the casting process may be
expressed, but the most common way of starting this
procedure to supply us your drawings and detailed specification of your product. Once we get
these drawings we get
in touch with customers design engineer and build an aluminium die with internal cavities that
will produce a wax
sample by injecting wax into the die. We send these wax patterns to customer and after approval
of wax patterns we
make sample casting. The wax patterns are attached to an assembly made from wax (called
cluster/tree) that allows
molten metal to enter, that produces a sound metal component